BURKHARDT+WEBER, an international manufacturer of machine tools, relies on condition monitoring with compacer
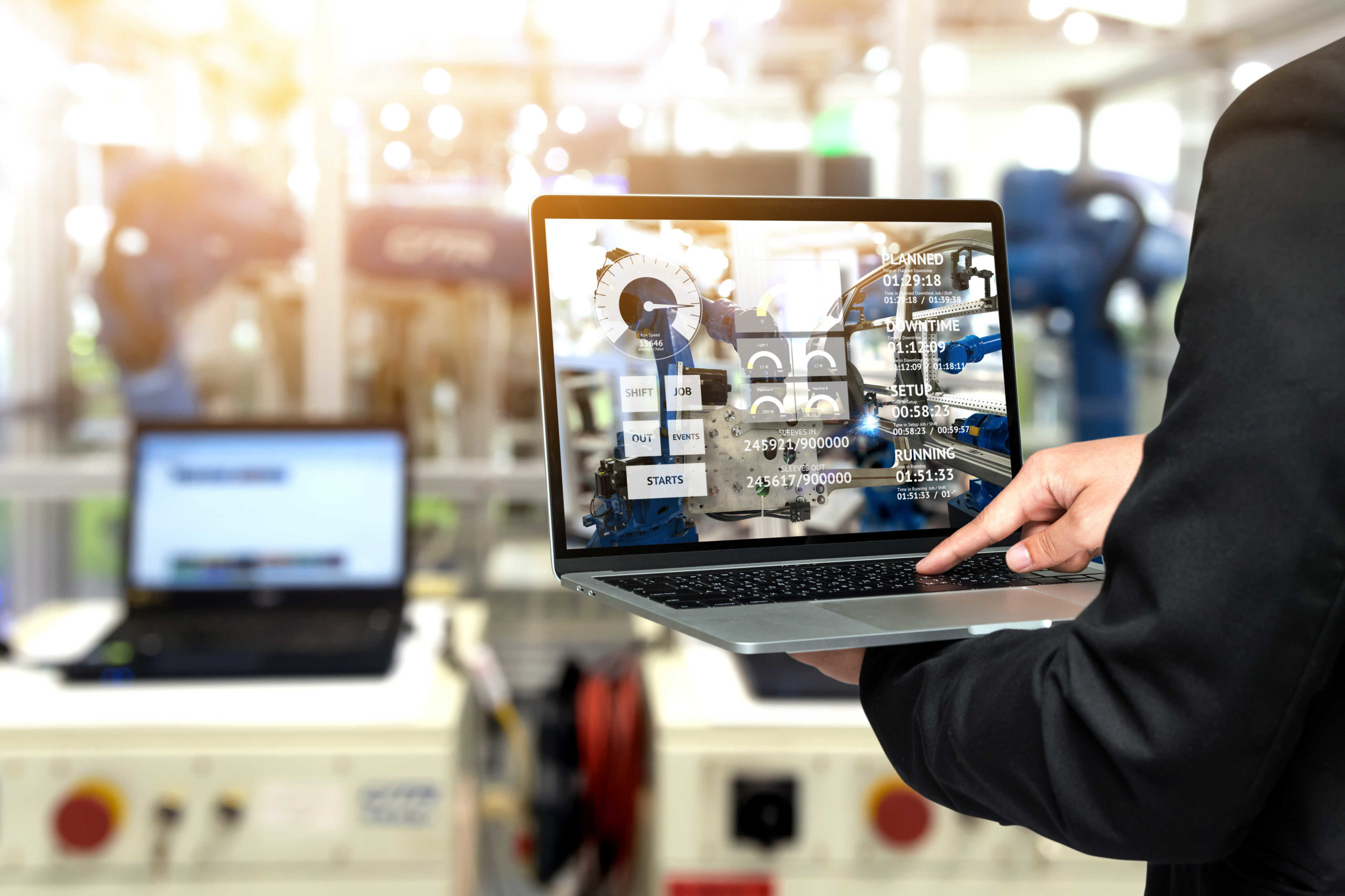
/Burkhardt-Weber/6cfe7f0c-5357-479b-93ca-29664f305a24.png)
Thanks to modern condition monitoring, the company saves costs that arise from unexpected maintenance failures and downtimes. The automated order suggestions, e.g. for defective parts, speed up production processes and make planning easier. The system can also be controlled remotely via an app.
"By integrating the compacer IIoT solution, we have not only added value to our systems, but also laid the foundation for new digital business models. This step is an important milestone in the direction of predictive maintenance."
In a production process geared towards efficiency and productivity, the individual production steps are closely interlinked. The sudden unexpected failure of a machine or component can bring the entire production line to a standstill.
In many manufacturing companies, heterogeneous production environments have grown over time and there are many systems with a low level of automation. These now need to be integrated into the new digital world.
Are you also thinking about connecting the old world with the new via an IT integration project?